- Home
- Blog
- High-Noise Workplace Safety
- How to Help Employees Follow OSHA Safety Rules?
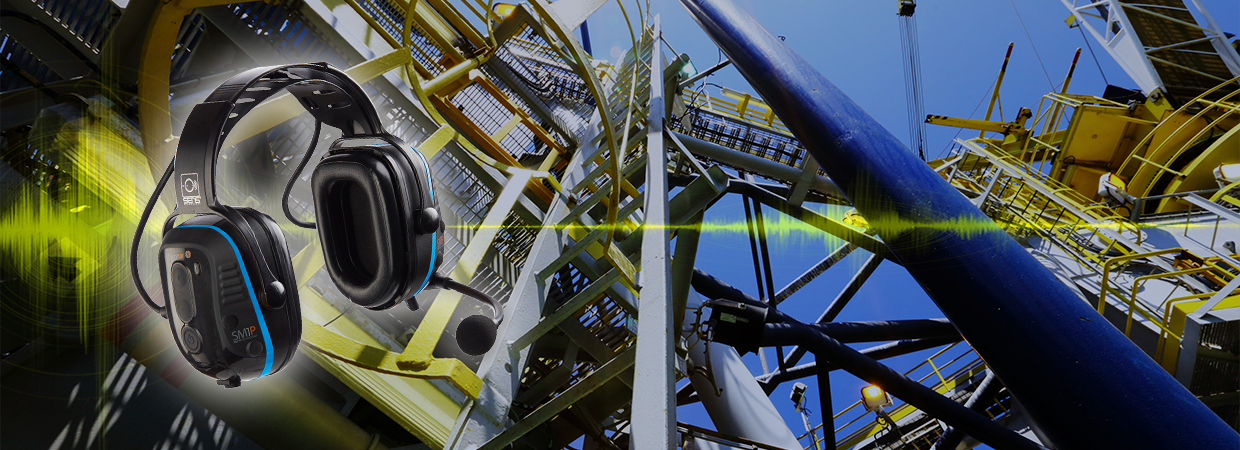
How to Help Employees Follow OSHA Safety Rules?
What Challenges are Safety Managers Most Concerned with?
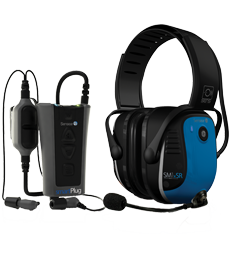
This is a question on everyone’s mind. A poll on the top challenges for 291 safety conducted by SafetyNewsAlert.com listed six main areas of concern. These ranged from “getting senior management to buy into safety” (19.2% listed as the top challenge) to “keeping safety costs in check” (8.0%).
One of the most interesting concerns ended up being noted as the biggest challenge to one in three safety managers: “employees.” The post then adds “safety training” (13.6%) to that number, resulting in the conclusion that about half the safety managers polled feel that combined, this is the biggest challenge.
Why?
- Provide a workplace free from serious recognized hazards and comply with standards, rules, and regulations issued under the OSHA Act;
- Make sure employees have and use safe tools and equipment and properly maintain this equipment;
- Establish or update operating procedures and communicate them so that employees follow safety and health requirements, and more.
Employers are required to adhere to a long list of OSHA standards and responsibilities, and maintaining employee compliance can be a significant challenge. One would think that a few rules that keep an employee safe at work would be an obvious reason to follow them. But so many don’t. According to an analysis by the American University Law Review, “in the construction industry, approximately 80% of job-related accidents were solely the result of employee failure to adhere to safety regulations.”
It’s clear to anyone who’s ever worked a job that people are constantly looking for faster and more efficient ways to do their job, yet sometimes that approach can lead to unsafe practices. In an executive report titled “Employees' Top 10 Safety Excuses – And How to Counter Them,” employees have a number of reasons why they don’t follow safety policies. Two examples include:
- The experienced employee (I’ve been doing this job like this for years), or;
- I’m young, and bad things happen to other people (It-won’t-happen-to-me).
This excerpt from the report provides a real representation of these two profiles (both don’t believe an injury will happen to them), what their perspective is on safety rules, as well as some great recommendations on how to address them.
What are Some of the Leading Ways and Best Practices to Help Employees Follow Safety Rules?
The report goes into deep detail, but the excerpt provides some great insight into places to start looking and questions to ask. These include:
- Are employees rewarded for completing a job faster?
- Are employees monitored for adherence to safety guidelines and OSHA standards?
- Does the company culture and values reinforce safety, or are safety rules and regulations seen as more of a nuisance?
- Do employees understand how a safe work environment not only impacts themselves but their fellow coworkers as well?
- Is there accountability for adhering to safety rules and regulations?
The report then explains some good approaches to addressing these challenges. For example, if you are rewarding fast production times, but not focusing on the safety aspect of the job, employees will value speed over adherence to safety guidelines, regardless of the standards in place. The suggested approach here is to reward adherence to safety rules “the same way meeting production deadlines are”.
Ultimately, there are some great suggestions for getting employees in line. They range from punishment (or reward), to bringing in someone who’s been seriously injured as an example to demonstrate the true negative impacts of not following safety guidelines to a young employee who feels invincible. There are more helpful suggestions in the excerpt and the report, and we talk more about How to Ensure the Use of Hearing Protection Devices here.
So what do you do when education, rewards, punishment, or a host of other tactics won’t get employees to follow safety guidelines? Or what if they believe that they’re being safe, but they aren’t? There are certain technologies out there that can proactively help safety managers help their employees adhere to OSHA regulations and guidelines.
Take for example the matter of protecting your employees’ hearing in high-noise work environments (you knew we were headed here didn’t you)? You invested in the latest technology: Bluetooth® digital headsets that have an NRR rating of 30. When you look out in the work area, all the employees are wearing them. Yet when you conduct your annual review, employees are still suffering from hearing loss.
How can this be?
How Can You Use Technology to Better Support Employees’ Adherence to OSHA Safety Standards?
Some safety devices leave a window of opportunity for employees to use the devices (adhering to the safety guidelines), yet also allow them to work around the device, or use it in a way that still results in unsafe conditions for them. In this instance, some of the best digital headsets allow you to increase the volume of the set to a level that’s STILL UNSAFE for the employee. So, while they are wearing the device and protecting their hearing from the external noise, they are using the protective device itself in a manner that results in hearing loss and circumventing safety procedures without even knowing it.
In this specific case, the employment of a hearing protection device (HPD), that has a built-in volume limiter, can prevent this exact issue from occurring. What good is a headset if it allows you to crank up the volume to levels that result in hearing loss and damage?
When you are planning your safety program and making technology acquisitions, it's useful to look for safety devices that not only meet OSHA’s standards but also support your workers in adhering to those standards. Products that are comfortable and convenient to use, that support different working styles, and that are equipped with technology that actually prevents them from side-stepping safety rules.
What techniques have you employed to get workers to adhere to OSHA’s standards or your safety program? Have you ever tried to bring in an injured employee as an example of what can happen when employees don’t follow safety guidelines?